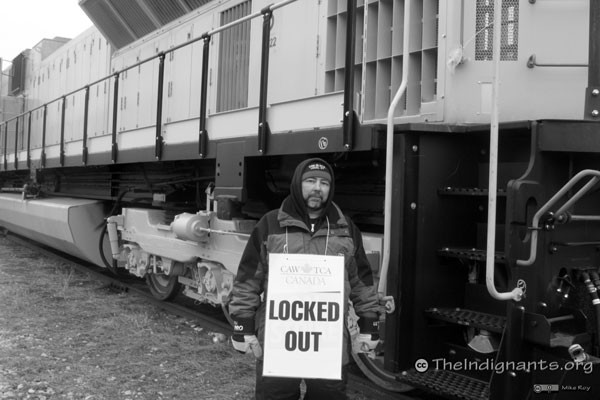
Rob almost doesn’t want to tell his friends he works at an autoparts plant. The reaction is so predictable. “There is this assumption that these are all still good jobs, that at least you’re unionized. And it’s like, ‘No, I’m getting paid just above minimum wage making drive shafts for American tanks.’”
The suburbs of Toronto and surrounding smaller cities, such as Oshawa, Guelph and London, are home to 88,000 workers in Ontario, about 40,000 of whom are organized with the Canadian Auto Workers (CAW). For unorganized auto workers, “Unstable work is the norm. When I left they laid off 100 people – that’s one plant. They had a meeting afterward and they said ‘this is seasonal, we have to do this every year,’” another auto parts worker, Yelena, told Briarpatch. “Factory work went from being this thing that you could get decent wages at … to being something that is seen as seasonal where a lot of the temp workers are hired for $12 an hour and not compensated for how dangerous your job actually is.” Temp pay can be little more than $10.25, minimum wage in Ontario. Hourly work can also be unstable and varies widely from plant to plant, with some workers having trouble getting enough shifts and others regularly forced to work excessive overtime.
Parts workers are routinely hired through temp agencies and forced to sign contracts that forbid them from taking a permanent job with the company, even though that condition violates Ontario’s labour laws. Once on the job, company contracts are often used as incentives, with companies sometimes “buying out” the contract from the agency after a few months. After that, the worker might end up as a company contract worker, with their three-or-six month probation period getting extended indefinitely. They sometimes end up working months or years as a temp. Any time workers take off, or mistakes they make in this years-long probation period can result in termination. Temporary and contract workers get few protections, even if they are in the union.
A temp worker, Derrick, was fired for missing a single day of work for a family health emergency. He was later held responsible for a workplace mistake that took place while he wasn’t working his station. Derrick discovered that he had been a member of CAW only when he received a second, amended T4 form including union dues that had not appeared on his paystubs. The union was unable to get him his job back, and his temp agency sent him an email indicating he had been blacklisted by the company.
The relatively high unionization rates in the sector do lead in some cases to the company forming “union-like structures” such as safety committees and occasionally even grievance procedures, but they are often staffed by management or secretarial workers. All the workers interviewed for this article talked about extreme heat in the plants, especially this past summer when high outside temperatures exacerbated heat from the machinery. Some plants had policies that allowed extra breaks if temperatures rose above 45 degrees Celcius. But the supervisors were the ones checking the temperature, which suspiciously hovered at 44 degrees for days. Parts workers said that the companies handed out free ice creams or freezies on extremely hot days, something the workers found extremely patronizing and an inadequate replacement for actual safety procedures.
Heat and exhaustion from forced overtime causes workers to make mistakes, increasing the risk of injury. Those Briarpatch spoke to recalled a variety of accidents, from pieces collapsing on them from 20 feet in the air, to workers being trapped in press machines, to electrocutions and press machines with broken light curtains (motion detectors that should stop the machine when a person is inside it). People recounted how injured workers are sometimes obstructed from filling out proper workplace safety and insurance board forms and forced to work while they are injured. Some are coerced into performing safety checks they don’t understand or aren’t qualified to do. One worker had been operating a piece of heavy equipment that had been leaking and unsafe for two years, and was unable to get anyone to fix it. Training is also inadequate. Workers say they either received no training or were trained by a temp with three days experience.
While some union plants consist almost exclusively of white workers born in Canada, Ian says that in his non-unionized parts plant, “like in most manufacturing environments, the workforce is majority immigrant, a majority are people of colour. The fact of the matter is that there is a very well-established informal hierarchy of who gets what kind of jobs, and who works on what shift.” He told Briarpatch the temp agencies that recruit these workers have huge presences in immigrant and poor neighbourhoods, whereas union halls do not.
Workers also spoke about resistance. They described in-formal direct action in the workplace to slow down the line or cause disruptions. But what about more formal organizing? Why aren’t the non-unionized workers unionizing?
Until unions can do more to protect their existing workers, the risks of unionizing are high and the benefits are hard to determine. As anti-union (ie. “right-to-work”) laws threaten to creep north from the United States to Ontario and Saskatchewan, these factory conditions will be the reality for more and more workers in Canada. This climate also puts additional pressure on unionized workers, resulting in sped-up production lines, lower wages, a lack of job security, and fewer benefits. It is becoming more difficult to even protect the union jobs that remain. If union jobs disappear, working and safety conditions would deteriorate even further for non-unionized workers.
The recent closure of the CAW-unionized Electro-Motive plant in London shows that unions have a long way to go if they want to challenge systemic problems in the auto industry. The closure of this plant coincided with an upsurge of activity from Occupy London, one of the more successful smaller-city Occupy movements. Members of Occupy London participated in a massive protest march against the closure of the Caterpillar plant. They broke off from the official union rally and marched eight kilometres out to the factory, helping to obtain a better severance package through an implicit threat that they would occupy the plant.
Briarpatch spoke with The Indignants, a media team consisting of Occupy London participants Mike Roy, Anthony Verberckmoes, and Curtis Nixon. They worked closely with labour leaders and rank-and-file workers with the goal of occupying the Electro-Motive factory, which they hoped would rejuvenate both Occupy and the labour movement in general.
“There was discussion about occupying the factory…but never anything official or above the table,” said Roy. “People were rather pumped about it. We actually got some civil disobedience training. And the day before it was going to happen, the rug got pulled out from underneath everyone’s feet.” The official explanation was that the threat of factory occupation was being used as a bargaining chip to get better settlements for the workers who were being fired. CAW national president Ken Lewenza was quoted in the Huffington Post on the non-occupation in London saying “we had the public’s attention anyway.” Herman Rosenfeld, a former CAW staffer and autoworker, spoke with London employees he had worked with years ago as a union rep at a plant in Scarborough. “Every single one of them, you talk to them and they say ‘well we didn’t want to turn people off, people were so supportive of us’. That said to me that that’s a failure in leadership… The union capitulated.”But given the general attention paid to Occupy back in January, the London plant had potential to be of importance across North America. “It was in a way a lost opportunity…Even if it had been a failed attempt to take the factory, it would have been such a message to other groups facing similar repression and similarly hard circumstances,” said Verberckmoes.
Rank-and-file workers can fight back, though. There was a wildcat action near London by CAW workers in St. Thomas, where an unfinished train made at the Caterpillar factory was blockaded by rank-and-file CAW workers who worked for another company. CAW went into negotiations this fall with the Big Three automakers (Ford, GM, Chrysler) with strike mandates of well over 90 per cent. Despite offering concessions like expanding the two-tier wage system by extending the amount of time it takes for new workers to climb the wage scale, the union still seems able to extract significantly higher wages and benefits than in the non-union parts sector. Nevertheless, they remain in a tight spot due to the huge concessions their American counterparts have taken and the inability of American unions to effectively fight anti-union legislation.
In the long term, the fate of CAW-unionized workers is going to depend on their ability to organize unrepresented parts and autoworkers. The wider the wage gap grows between unionized and non-unionized workers, the more concessions CAW autoworkers will have to endure.
These unorganized workers are the ones who have been left behind – willingly or not – by the unions, and go unnoticed by the rest of society. They are providing the workforce for an auto sector that is still vital to the economic existence of smaller cities in southern Ontario.
Names of all auto workers quoted in this piece have been changed due to job insecurity in the sector.